CrossTEQ Quality Management
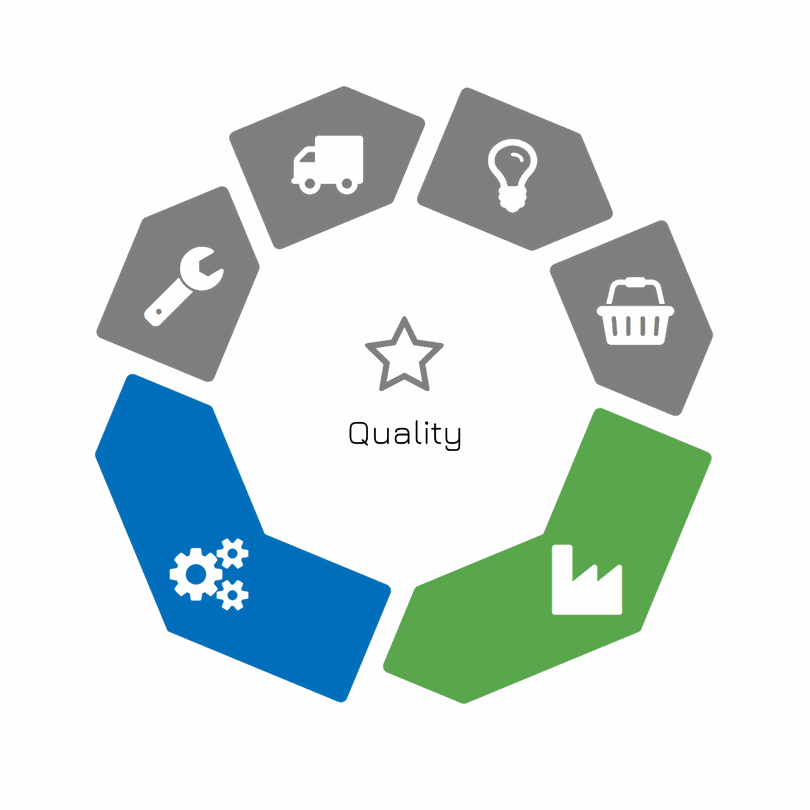
Processes
We comply with all ISO 9001 standard requirements and are committed to their practical implementation in all areas of our company. Every manufactured system or subsystem is subject to strict quality monitoring.
Infrastructure
Thanks to completely digitized production processes and a highly secure IT infrastructure, all data is digitally and consistently documented and permanently monitored. This enables us to detect errors and risks immediately and to trace back deviations without gaps.
Employees
Through regular training of our employees, we promote a common understanding of quality and permanently ensure the highest quality and precision at the cutting edge of technology.
Communication
Together with our customers, employees and suppliers, we want to cultivate a common understanding of quality. To this end, we actively promote a transparent and systematic exchange of information with our stakeholders.
Supply Chain
With the claim to be able to offer our customers a reliable and seamless service with the highest quality and flexibility on a permanent basis, we have been relying on secure and long-term supply sources and a state-of-the-art EDI infrastructure for years.
Quality planning
- Wir definieren Leistungsmerkmale individuell für jedes Produkt und gemäss den spezifischen Anforderungen unserer Kunden.
- Wir planen, implementieren und optimieren Produktionsprozesse entsprechend. Die Bedürfnisse unserer Kunden stehen dabei immer an erster Stelle.
- We design requirement catalogs, comprehensive process descriptions and product-specific work and assembly instructions to ensure the highest quality and process reliability.
- We establish effective quality tests.
Qualitätslenkung und Product Data Management
Wir dokumentieren und überwachen konsequent sämtliche Daten und alle Produktionsprozesse auf unserer sicheren IT-Infrastruktur. Dadurch gewährleisten wir:
- Einen nahtlosen Informationsfluss mit unseren Kunden, Lieferanten und Mitarbeitern in Echtzeit
- Lückenlose Zurückführung von Material, Bauteilen, Abweichungen und Ausfällen
- Die sofortige Erkennung von Fehlern und Risiken
- Die kontinuierliche Verbesserung der Prozesse durch das Erkennen von Potentialen und Lernen durch Fehler.
Quality assurance
Durch regelmässige Qualitätsaudits und Schulungen stellen wir sicher, dass unser eingespieltes Team aus qualifizierten Ingenieuren, Fertigungstechniker und Montage-Experten ein gemeinsames Qualitätsverständnis pflegt und der konsequenten, operativen Umsetzung der ISO:9001 Normanforderungen verpflichtet bleibt.
Thus, our employees are trained and qualified in dealing with:
- Top-secure, digital infrastructure and state-of-the-art technical and IT equipment
- Material analyses and quality tests (functional, burn-in and factory acceptance tests)
- Komplett digitalisierte Dokumentation und PDM
- Berichterstellung an Sie und unsere, bzw. Ihre Lieferanten
Quality improvement
Within the framework of continuous quality improvement, preventive measures are taken to prevent the recurrence of an error once it has been detected.
Customer complaints, product defect reports, defect logs and audit reports are regularly evaluated to eliminate causes of defects.
The necessary measures are defined by management and their implementation is monitored. The effectiveness of preventive measures is reviewed at appropriate intervals.
Methods to be used from which preventive measures are generated:
- Sammlung von Erfahrungen aus vorangegangenen Projekten
- Internal audits and process evaluations
- Preventive maintenance of machinery, equipment and facilities
- Integration of customer complaints and error images from production into new product designs
- Risikobetrachtungen mittels FMEA (Failure Mode and Effects Analysis)
Qualitätspolitik
The common mission of the CrossTEQ divisions involves the consistent alignment of our core competencies with the high quality and service requirements of our customers, with the aim of achieving their maximum satisfaction.
- Execution of orders on time at any time in perfect and lasting quality is a company principle for us.
- Mit unseren umfassenden und flexiblen Servicelösungen wollen wir uns langfristig und mit maximalem Projektfokus für den Erfolg unserer Kunden engagieren.
- The stable quality of our development, manufacturing and testing services is the foundation of our successful business activities.
- For us, quality means meeting both expressed and unspoken customer expectations and, if economically possible, exceeding them.
- Unsere Qualitätsbestrebungen erfolgen in Übereinstimmung mit Gesetzen und nach den Forderungen der DIN EN ISO 9001:2015 und einer zweckmäßigen Prüfplanung.
Our employees
- Each employee has a special responsibility for his or her professional activity.
- Only qualified and trained employees guarantee the agreed services in professional terms. Therefore, we keep ourselves up to date through continuous training. We regularly determine employee satisfaction and take the results into account in further employee planning as well as in the design of workplaces.
- Employees are provided with positive framework conditions to strengthen employee motivation and employee satisfaction. Our employees are obliged to actively participate in the maintenance and improvement of the quality management system.
- All our employees strive to ensure consistently high quality in the interest of our customers.
- The constant flow of information between management and employees ensures an open and honest working atmosphere. The error culture, which is based on a positive view of human nature and to which every employee contributes, supports this positive climate.
Unsere Lieferanten
- Auch Kooperationspartner sind zur Einhaltung von vereinbarter Qualität verpflichtet.
- We monitor and support their activities to avoid any negative impact on our quality.
Qualität liegt in unserer DNA
We want to support Swiss technology providers in the development and implementation of their ideas and products and be a reliable partner close to them.
We strive to meet the expressed and unspoken expectations of all our company's stakeholders - but especially those of our customers and employees.
In an open and dynamic dialog, we want to challenge and sharpen our common understanding of quality on a daily basis and thus create the basis for fruitful cooperation and sustainable success on all sides.
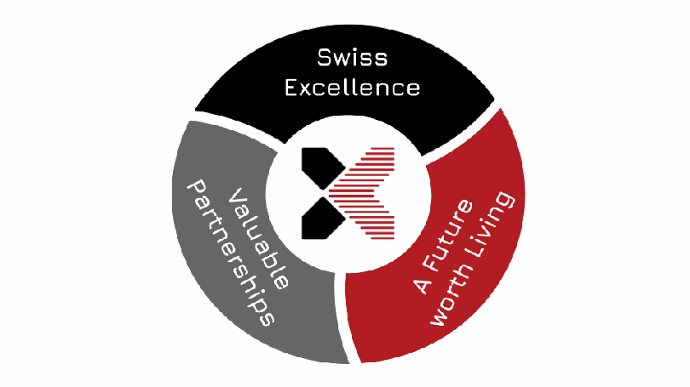